Material handling equipment services
Material handling equipment services encompass a wide range of services designed to keep your essential machinery running smoothly.
Whether it’s forklifts, conveyor systems, pallet jacks, or automated storage and retrieval systems, this equipment is vital for operational efficiency. However, like any other machinery, material handling equipment requires regular maintenance and service to perform at its best and to avoid costly downtime.
Why choose Lödige Industries’s for your material handling equipment service?
Lödige Industries provides bespoke maintenance services for material handling equipment, which guarantee your assets operate reliably and at the lowest possible cost. At the same time, our international service network ensures a fast response in the event of spontaneous faults even for equipment not delivered by Lödige.
As your needs change over time, Lödige can also support the expansion of your facility, or the transition to new technologies. We have a strong track record for delivering material handling systems enhancements or modernisations whilst clients continue to run their day to day business.
MAINTENANCE - Maximise reliability and safety of your material handling system
Field service
Our field service offers the following on competitive unit rates or based on a fixed monthly fee, depending on your requirements:
- Preventive Maintenance;
- Breakdown and Repairs Call Out;
- Predictive Maintenance;
- Programmable Device support;
- Compliance with Safety Requirements;
- Scale calibration and certification services;
- Professional Engineer services;
- Ad hoc support for your existing maintenance team.
Residential Service
Our Residential Service product provides a managed, comprehensive maintenance service designed to maximise overall system availability and reduce overall cost, delivered by a team of experienced and highly trained maintenance technicians based on your site.
Services provided under this product are tailor made to suit but can typically include:
- Preventive Maintenance;
- Predictive Maintenance;
- 24 hr Breakdown and Repairs;
- Computerised Maintenance Management Systems (CMMS);
- Support for all programmable devices;
- IT Application & Hardware, Network / LAN Support;
- Spare Parts;
- SCADA operations;
- Specialist Engineering Services;
- Compliance with safety requirements;
- Scale calibration and certification services;
- Professional Engineer services.
MODERNISATION - Improving the performance and energy efficiency of your material handling system
We can perform the following common system modernisations:
- PLC upgrades (Siemens, Allen Bradley, Mitsubishi, Omron, etc.);
- Mobile equipment (hoists, transfer vehicle, SRM) overhaul or replacement;
- DC to AC drive conversion;
- Safety system upgrades;
- Horizontal & vertical speed / positioning system upgrades;
- SCADA system upgrades;
- Sensor upgrades.
Typical System enhancements may include:
- Integration of additional storage, conveying or throughout capacity;
- Integration of additional weighing, bar code scanning, cool room facilities etc.;
- Integration of vertical conveying capacity;
- Integration of X Ray machines;
- Conversion of unpowered to powered conveyors;
- IT application replacement;
- Process optimisation;
- Equipment dismantling, relocation.
All modernisation projects take into account:
- Concept / Layout design;
- Car parking processes;
- Mechanical design & integration;
- Electrical design & integration;
- PLC programming;
- IT networks, platforms, peripherals and software applications.
SPARE PARTS & REPAIR - Genuine spare parts and components
Services offered:
- Supply of genuine Lödige parts;
- Supply of genuine OEM parts;
- Specification and supply of recommended spare parts packages;
- Obsolete / Legacy part migration;
- Parts repair and refurbishment.
In addition, expert Lödige technicians can be quickly dispatched to your site to deal with emergency breakdowns directly or to support your local maintenance team as required.
Leveraging our know-how to boost your success
We can advise you on:
- Maintenance optimisation – cost vs performance;
- Maintenance outsourcing – focus on your core business;
- Operational process optimisation – get the best out of your material handling system;
- Control system upgrades – to the latest state of the art;
- Equipment refurbishment / replacement – increasing performance and reliability;
Contact us to arrange a meeting to talk through your needs
Find out more about Lödige servicing
-
Technology in Motion
Lödige Industries at a glance
Please contact us
We look forward to your message.
Frequently Asked Questions (FAQs)
Material handling equipment refers to machines, tools, and vehicles used to move and store materials and products in various industries. This can include forklifts, cranes, conveyors, pallet jacks, and automated systems.
Regular service is crucial for material handling equipment to ensure its optimal performance, reliability and safety. It helps identify and address any potential issues before they become major problems, reducing downtime and minimising the risk of accidents.
Preventive maintenance helps extend the lifespan of equipment, enhances its efficiency, reduces unexpected breakdowns, lowers repair costs and improves overall productivity. It also ensures compliance with safety regulations and standards.
The frequency of servicing material handling equipment depends on several factors. These include the type of equipment, intensity of use, manufacturer's recommendations and environmental conditions. Generally, it is recommended to have routine maintenance performed quarterly, semi-annually, or annually.
A material handling equipment service typically includes inspections, lubrication, adjustments, component replacements, cleaning and performance testing. It involves checking for worn-out parts, verifying fluid levels, assessing electrical systems and addressing any specific issues reported by equipment operators.
Some common signs that your material handling equipment may need servicing include unusual noises, decreased performance, erratic movements, leaks, warning lights or error messages. If you notice any of these signs, it is advisable to schedule a service promptly.
Looking for Material Handling Systems?
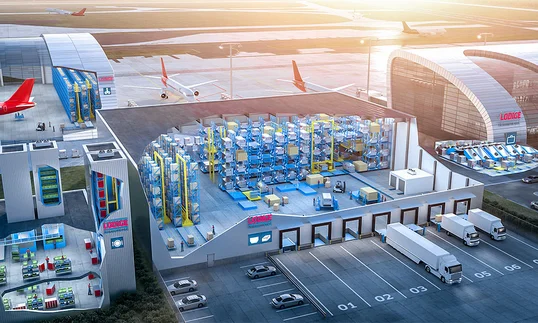
Quality, throuput and reliability with aiport logistics from the market leader
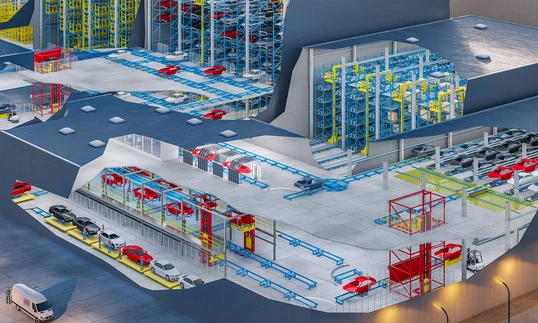
Quality, throuput and reliability with aiport logistics from the market leader